Solution overview
Maximising the utilisation and efficiency of your assets is key to gaining a competitive advantage. The Predictive Maintenance module for Dynamics 365 Unified Operations enables manufacturers to move from a reactive to proactive model of maintenance.
Predictive Maintenance component overview
Component failure often causes unplanned downtime, disrupts production plans and can even be a safety risk. Manufacturers can move to a more effective maintenance strategy by collecting data from connected devices and transforming it into valuable business intelligence to automate service calls, reduce downtime and save costs.
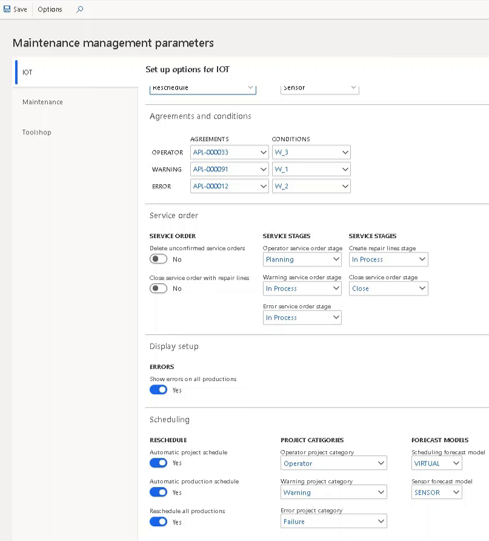
Predictive maintenance optimises the balance between corrective and preventative maintenance, using the power of machine learning to enable just-in-time replacement of components, only replacing them when they are close to failure. Extending the lifespan of components and decreasing unscheduled maintenance and labour costs delivers savings and competitive advantages.
Predictive Maintenance features
The Predictive Maintenance module allows Dynamics 365 to automatically:
- Inform machine operators of technical status and possibility of breakdown
- Create service orders based on direct machine data or operator intervention
- Trigger a visual signal on the machine or predictive maintenance dashboard
- Reschedule production orders
- Switch off the machine in case of a breakdown or possibility of a breakdown
- Plan maintenance based on maintenance interval parameter or machine safe operation time
The module also supports tool rental, and controls whether tool rental will affect the production plan, synchronising tool rental with production resources and the Fixed Assets module.
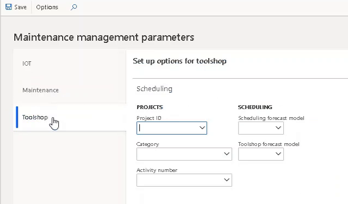
The Predictive Maintenance module enables your Dynamics 365 system to automatically launch operations by collecting and processing both internal system data and external data. When scheduling maintenance the system will also take into account any materials that need replacing or replenishing, such as filters, lubricants, oils and other consumables.
Challenges
Companies often struggle with rising maintenance costs. Predictive maintenance allows for more efficient planning of repairs and part replacements, which can reduce costs.
Not only are direct maintenance costs rising, but also downtime costs. Production interruptions are costly, and predictive maintenance can help avoid unplanned downtime.
Maintenance is often performed either too early or too late. A lack of precise knowledge about the condition of machines leads to inefficient use of resources.
Downtime and machine failures reduce factory productivity. Predictive maintenance can help minimize these issues.
Fatigue among maintenance teams can lead to accidents. Additionally, a lack of knowledge and difficulties in staffing maintenance positions pose a challenge for many companies.
Advantages
Predictive maintenance allows for the detection of potential machine and equipment issues before failures occur, significantly reducing production downtime.
By detecting problems early, companies can avoid costly emergency repairs and equipment replacements.
Detecting and fixing problems before they become serious can prevent failures that could be dangerous for employees.
Regular monitoring of equipment condition enables the optimization of their performance, leading to increased overall productivity.
Regular maintenance and repairs based on predictions can significantly extend the lifespan of equipment.
Predicting maintenance needs allows for better management of spare parts inventory, which can lead to significant savings.